|
 |

Fieldbus & Device Networks
While the network technologies described so far are typical for business information systems, they are converging with industrial instrumentation and control systems. Industrial plants have used information technology (IT) for years, but with open IT standards, faster computers, emerging software, and demand for integrated information by all segments of an industrial enterprise (accounting, engineering, operations, maintenance, and management), industrial networks are merging right into enterprise-wide IT solutions.
PLCs and distributed control systems (DCSs) are offering Ethernet/ TCP/IP connectivity so that real-time information on plant processes is readily accessible by any workstation on the network (LAN or WAN), in a client-server relationship. A plant manager can watch a graphic display of plant operations in one window while scanning accounting data in another.
Object Linking and Embedding (OLE) and Dynamic Data Exchange (DDE) can merge data streams, such as unit cost (from accounting) and production totals (from the plant floor) in one spreadsheet. Internet and intranet browsers running Java or HTML applications access data acquisition and control systems using standard LAN/WAN technologies.
Meanwhile, on plant and factory floors, industry has developed its own range of fieldbus or device-level networks for linking control devices with increasingly intelligent instrumentation. As the terms have evolved over the past several years, device networks typically embrace those optimized for discrete manufacturing automation, while fieldbus connotes more process-oriented instrument networks. On the discrete side, the emphasis is on high-speed transmission of typically smaller information packets. Process fieldbuses, on the other hand, sacrifice speed for more secure transmission of larger information packets. Intrinsically safe capabilities also are prerequisite for many process applications.
An exhaustive comparison of the 20-some device and fieldbus protocols currently available is beyond the scope of this volume. However, an examination of two leading alternatives, the Profibus family of automation networks and the Foundation process automation protocol, illustrates the essential concepts of both types of networks.
The Profibus Family
Profibus is a fieldbus and device network technology used primarily in Europe, but gaining worldwide acceptance. The Profibus family follows an open network standard (EN 50 170) with hundreds of vendors supporting a common, interchangeable interface and protocol.
Profibus PA-Process Automation. Allows sensors and actuators to be connected on one common bus line, even in intrinsically safe areas.
Profibus DP-Factory Automation. Optimized for high speed and inexpensive connectivity (plug and play). Designed for communication between automation control systems and distributed I/O at the device level.
Profibus PA-Process Automation. Allows sensors and actuators to be connected on one common bus line, even in intrinsically safe areas.
Profibus DP-Factory Automation. Optimized for high speed and inexpensive connectivity (plug and play). Designed for communication between automation control systems and distributed I/O at the device level.
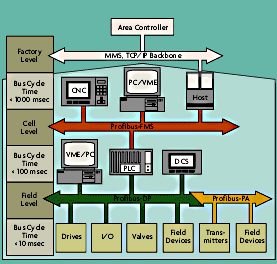 |
Figure 4-10: Profibus Applications |
Profibus FMS-Automation for General Purposes. Designed for a large number of applications and communications at the cell level.
Profibus is basically a serial bus system with which digital controllers can be networked together with master and slave devices over a pair of wires. Masters, or active stations, control the data communication on the bus. They can send messages without an external request by holding bus access rights by way of a token. Slaves, or passive stations, are peripheral devices that may include input/output (I/O) modules, valves, drives, and transmitters. Slaves do not have bus access rights; they can only acknowledge received messages or send messages when the master requests one.
The Profibus protocol varies with each member of the family (Figure 4-11).
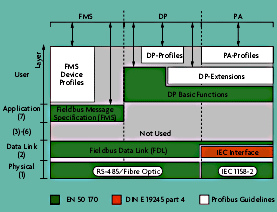 |
Figure 4-11: Protocol Architecture of Profibus |
Profibus DP uses the physical and data link layers (1 and 2), coupled to a user interface, for fast and efficient data transmission. Layers 3 through 7 are not defined. A Direct Data Link Mapper (DDLM) provides access between the user interface and the data link layer. Application functions are defined in the user interface. The physical layer is defined via the RS-485 or fiber optic transmission technologies.
Profibus FMS defines the physical, data link, and application layers. Layers 3 through 6 are not defined. The application layer combines the Fieldbus Message Specification (FMS) and a Lower Layer Interface (LLI). FMS runs the application protocol as well as supporting communication services. The LLI implements communications and provides device-independent access to the Fieldbus Data Link (FDL) at layer 2. Layer 1 is implemented again in RS-485 or fiber optics.
Profibus PA is an extension of the Profibus DP protocol for data transmission. Layer 1 (physical) in this standard uses IEC 1158-2, which provides intrinsic safety and Òpower on the busÓ for field devices. 1158-2 modulates a steady-state 10 mA dc Òbasic currentÓ (the bus power) by Manchester encoding a ±9 mA dc signal on top of the basic current.
Manchester encoding refers to a signaling technique that produces binary ones and zeroes by transitioning between high and low signals (+9 mA dc to -9 mA dc in the 1158-2 case) over an elevated steady-state voltage or current. A high-to-low transition is a one, and a low-to-high transition is a zero. Thus, every bit period has a transition in it, allowing the receiver to synchronize easily with the transmitter. One disadvantage is that it requires twice the bandwidth as straight binary encoding.
Profibus DP and Profibus PA can be integrated via a segment coupler. And because Profibus DP and Profibus FMS use the same transmission technology and a uniform bus access protocol, they can be operated simultaneously on the same cable.
Foundation Fieldbus
The Fieldbus Foundation is a worldwide consortium of manufacturers and industry groups that have designed and manufactured another open fieldbus technology called Foundation. Software and hardware specifications have been written by design and marketing teams, and many products are becoming available that conform to this standard across many different vendors.
The Foundation protocol (Figure 4-12) uses layers 1, 2, and 7 (physical, data link, and application layers). Layers 2 and 7 are considered bundled together in a communication stack.
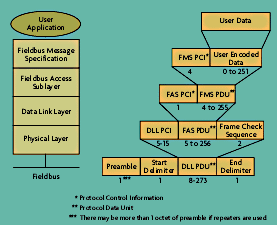 |
Figure 4-12: Foundation Fieldbus Protocal Stack |
Foundation and Profibus look similar at first. On the physical layer, the main differences are in signaling methods. Foundation offers IEC 1158-2 signaling, like Profibus.
Foundation also offers a 31.25-kbps option, as well as 1.0 and 2.5-Mbps options. The 31.25-kbps version uses a Manchester encoding scheme (±10 mA dc into 150 ohm load) that can use existing 4-20 mA twisted pair wiring. With an intrinsically safe IS) barrier, the 31.25-kbps option supports intrinsic safety. The dc supply voltage ranges from 9 to 32 volts, but may be restricted to the barrier rating. Stubs or spurs are allowed, from 1 meter to 120 meters depending on the number of devices on the bus.
The 1.0 and 2.5-Mbps options both offer voltage mode signaling. The 1.0-Mbps option also allows current mode signaling. The voltage mode method delivers ±60 mA dc into a 75-Ohm equivalent load, while the current mode signaling method modulates the fieldbus signal on top of a 16-kHz ac power signal.
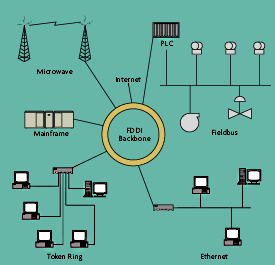 |
Figure 4-13: Typical Enterprise Network |
The Foundation communication stack is comprised of layers 2 and 7 in the OSI model. Layers 3 through 6 are not used. The Data Link Layer, or DLL, controls message transmission on the bus through a Link Active Scheduler (LAS). Link Masters and Bridges are used to control and extend the bus.
The Fieldbus Access Sublayer (FAS) works with the Fieldbus Message Specification (FMS) to form an application layer, just underneath the user application. The FAS services are described via Virtual Communication Relationships (VCRs). The VCR is like a speed-dial feature on a telephone, used for communicating quickly and easily to another fieldbus device. Three VCR types, Client/Server, Report Distribution, and Publisher/Subscriber are used for operator messages, event notification and trend reports, and data publishing, respectively.
The Fieldbus Message Specification (FMS) communicates via data objects and function blocks over the bus. FMS can only use the client/server VCR type.
User applications in the Fieldbus protocol use standardized function blocks for I/O engineering unit conversion, and common functions like PID control.
|
References and Further Reading |
|
The Data Acquisition Systems Handbook, Omega Press LLC, 1997. |
|
New Horizons in Data Acquisition and Computer Interfaces, Omega Press LLC, 1997. |
|
Omega® Universal Guide to Data Acquisition and Computer Interfaces, Omega Press LLC, 1997. |
|
Business Data Communications, Fourth Edition, D. A. Stamper, Benjamin/Cummings, 1994. |
|
Computer Networks, Second Edition, A. S. Tanenbaum, Prentice Hall, 1988. |
|
Data Communications - Video and Workbook, by Industrial Training Corp. for ISA, 1993. |
|
Data Communications, Computer Networks and Open Systems, Fourth Edition, F. Halsall, Addison-Wesley, 1996. |
|
Distributed Systems - Concepts and Design, Second Edition, G. Coulouris, J. Dollimore, and T. Kindberg, Addison-Wesley, 1994. |
|
Guide to Networking and Internetworking Terms, P. Simoneau, American Research Group, 1994. |
|
How Networks Work, F. J. Derfler, Jr., and L. Freed, Ziff-Davis Press, 1993. |
|
Technical Overview: Foundation Fieldbus,
Fieldbus Foundation, 1996. |
| |
|