|
 |

Previous chapters of this volume have acquainted you with the technology of how input/output (I/O) signals are generated, conditioned, linearized, and transmitted to a host computer or controlling system. In this chapter, we will look at the different kinds of data acquisition hardware that are available to help you perform all of these functions.
Before starting, a brief good news/bad news observation: The good news is that modern microcomputer technology has made it relatively simple to install, configure, and start up a high-performance data acquisition system. Experienced users will be happy to know that many of the problems encountered a few years ago are gone. New users will never realize how difficult it once was to bring up a data acquisition system. The bad news is that these same technology advances have made it even more difficult than ever to select among the many options. The hardware decisions facing a user today require a great deal of study, analysis, and consideration. Every system will work, but some are better than others for each particular application.
Some things to consider:
Connect to the Internet or an intranet? Today, users can obtain real-time data over the Internet or an in-house intranet, using a standard browser, an Ethernet connection or modem, and a PC or network computer (NC). A network computer has no moving disk to store programs. Instead, it downloads various software packages in the form of "applets" to the NC when needed. This means that your real-time data can be viewed by anyone in the world (if they have the proper access). The argument for using NCs is powerful. It could affect your choice of hardware.
What PC interface? Virtually all objections to using PCs on the plant floor have been answered, and PCs are now performing everything from real-time control to high-speed data acquisition. One major issue to be considered is the various bus architectures available for PCs. While we will discuss the various computer buses below, you may want to explore this topic in more detail to determine the effect it may have in your application, now and in the future.
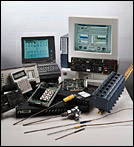 |
Commercially available data acquisition systems and components come in a wide variety of configurations and form factors. |
Is there software support? Most data acquisition hardware is compatible with most popular industrial software, or it comes with a software package of its own. Free or not, it is a good idea to investigate the software and hardware's capabilities. (For more details on software selection criteria, see Chapter 6.)
Selecting a System
It is possible to select a wide range of different products and configurations that will acquire and process data equally well. These range from field-mounted individual devices-such as DIN-rail signal conditioners or smart transmitters-to plug-in data acquisition systems that can be installed in a PC.
Virtually all these data acquisition devices and systems have the same basic specifications and options on their data sheets:
Signal conditioning: The signal from any sensor must be converted from its analog form into a digital signal that the host computer or controller can understand. This can be done by a transducer or transmitter in the field, a local signal conditioner, or-if close enough-by the analog-to-digital (A/D) converter on a data acquisition board. In addition, signals from nonlinear sensors, such as differential pressure flowmeters and thermocouples, must be linearized. If the environment is particularly noisy, these conversions should be done as close to the sensor as possible.
Number of analog input channels: Analog inputs usually are specified as single-ended or differential input channels. Single-ended (SE) channels all reference the same ground point. Differential inputs (DE) have different reference points for each input, and therefore need two channels. In general, SE channels are appropriate when the input signals are greater than 1 V, the signal source is no more than 15 feet away, and all inputs share a common reference. DE inputs have better noise immunity and help prevent ground loops.
Sampling rate: This determines how fast an analog signal is converted to digital. In general, select a sampling rate that is twice as fast as you need. The operating software of most PC systems causes skew to occur. Skew can approach or even exceed the sampling interval. When this happens, patterns in the data may no longer be accurate or reliable.
Resolution: This determines the smallest value change the system can detect. Most systems have 12 or 16-bit resolution; a 12-bit system resolves 1 part in 4,096, while a 16-bit system resolves 1 part in 65,536. The resolution in engineering units is determined by dividing the measurement span by 4,096 (or 65,536). For example, if you are measuring a voltage signal of 0-1,000 V with 16-bit resolution, the smallest change the system can see is ±0.2 V (or ±0.015 V).
Accuracy: This is a function of many variables in the system, including A/D nonlinearity, amplifier nonlinearity, gain and offset errors, drift, and noise. (See further discussion in the "High-Accuracy Data Acquisition" section that follows.)
Analog inputs: Typical voltage inputs are 0-1 V, 0-10 V, ±50 mV, ±100 mV, ±0.5 V, ±5 V, and ±10 V. Other inputs include 0-20 mA, 4-20 mA, frequency, and resistance. Most of the big four process control measurements-flow, temperature, pressure, and level-fit one or more of these input ranges. Most data acquisition products have selectable or programmable analog inputs that accept the signal, and send it to a 12- or 16-bit A/D converter.
Analog outputs: While not strictly part of data acquisition, many data acquisition products offer analog outputs on the same board. In almost all cases, a data acquisition board has either 2 or 4 outputs. If more are needed, a dedicated analog output board may be required.
Digital I/O: Most digital I/O can be selected for either input or output. In most cases, it is possible to configure a data acquisition board with digital inputs, outputs, or both in any combination. Boards that claim to be "multifunctional" have the most digital I/O.
In addition to comparing basic specs, examine how the product is designed and built. Accuracy is often dependent upon the amount of noise picked up by the system. Modern data acquisition products minimize this problem in several ways:
Surface mount technology (SMT): Using SMT shortens the length of traces on the board, which improves electrical noise resistance.
ASICs: Application specific integrated circuits (ASICs) combine the functions of several components into one. They also eliminate the connections between those individual devices, increasing speed, improving accuracy, and reducing exposure to noise.
Reduced board size: With today's SMT and ASIC technology, many data acquisition boards are being made in a smaller size (form factor). Once again, reducing the size and number of traces boosts speed and minimizes noise.
Isolated inputs: Input isolation protects the board from damage or disruption from an abnormal signal or noise on the input line.
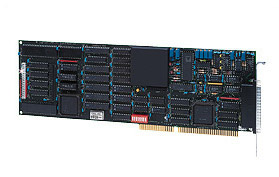 |
Typical ISA-bus data acquisition board plugs into a standard PC and offers a variety of speed, resolution, and other feature options. |
Finally, you have to decide what type of data acquisition system to use. There are two major choices:
Plug-in data acquisition cards: These plug directly into the chassis of your computer. Signals from sensors or signal conditioners are wired to the computer and connected to the data acquisition board.
Standalone systems: Self-contained I/O systems acquire data in the field, and send it to the computer via a network or communications method of some kind.
Let's look at both types.
|