Why should I use an infrared pyrometer to measure
temperature in my application?
Infrared pyrometers allow users to measure temperature in
applications where conventional sensors cannot be employed.
Specifically, in cases dealing with moving objects ( i.e., rollers,
moving machinery, or a conveyer belt), or where non-contact
measurements are required because of contamination or
hazardous reasons (such as high voltage), where distances
are too great, or where the temperatures to be measured are
too high for thermocouples or other contact sensors.
What should I consider about my application when selecting
an infrared pyrometer?
The critical considerations for any infrared pyrometer include
field of view (target size and distance), type of surface being
measured (emissivity considerations), spectral response
(for atmospheric effects or transmission through surfaces),
temperature range and mounting (handheld portable or
fixed mount). Other considerations include response time,
environment, mounting limitations, viewing port or window
applications, and desired signal processing.
FIELD OF VIEW
What is meant by Field of View, and why is it important?
The field of view is the angle of vision at which the instrument
operates, and is determined by the optics of the unit. To
obtain an accurate temperature reading, the target being
measured should completely fill the field of view of the
instrument. Since the infrared device determines the average
temperature of all surfaces within the field of view, if the
background temperature is different from the object
temperature, a measurement error can occur (figure 1).
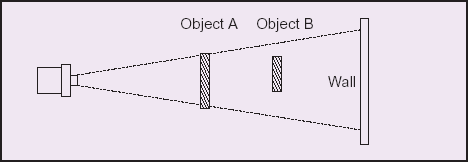
Figure 1: Field of view
Most general purpose indicators have a focal distance
between 20 and 60". The focal distance is the point at which
the minimum measurement spot occurs. For example, a unit
with a distance-to-spot size ratio of 120:1, and a focal length
of 60" will have a minimum spot size of 0.5" at 60" distance.
Close-focus instruments have a typical 0.1 to 12" focal length,
while long-range units can use focal distances on the order
of 50'. Many instruments used for long distances or small
spot sizes also include sighting scopes for improved focusing.
Field of view diagrams are available for most instruments to
help estimate spot size at specific distances.
EMISSIVITY
What is emissivity, and how is it related to infrared temperature measurements?
Emissivity is defined as the ratio of the energy radiated by
an object at a given temperature to the energy emitted by
a perfect radiator, or blackbody, at the same temperature.
The emissivity of a blackbody is 1.0. All values of emissivity
fall between 0.0 and 1.0.
Emissivity (ε), a major but not uncontrollable factor in IR
temperature measurement, cannot be ignored. Related to
emissivity are reflectivity (R), a measure of an object’s ability
to reflect infrared energy, and transmissivity (T), a measure of
an object’s ability to pass or transmit IR energy. All radiation
energy must be either emitted (E) due to the temperature of
the body, transmitted (T) or reflected (R). The total energy, the
sum of emissivity, transmissivity and reflectivity is equal to 1:
E + T + R = 1.0
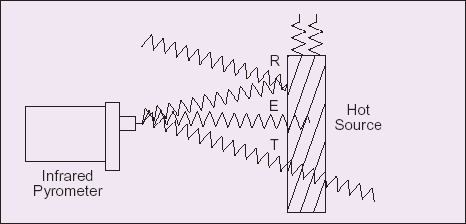
Total infrared radiation reaching pyrometers
The ideal surface for infrared measurements is a perfect
radiator, or a blackbody with an emissivity of 1.0. Most objects,
however, are not perfect radiators, but will reflect and/or
transmit a portion of the energy. Most instruments have
the ability to compensate for different emissivity values,
for different materials. In general, the higher the emissivity
of an object, the easier it is to obtain an accurate temperature
measurement using infrared. Objects with very low emissivities
(below 0.2) can be difficult applications. Some polished, shiny
metallic surfaces, such as aluminum, are so reflective in the
infrared that accurate temperature measurements are not
always possible.
Reflectivity is usually a more important consideration than
transmission except in a few special applications, such as
thin film plastics. The emissivity of most organic substances
(wood, cloth, plastics, etc.) is approximately 0.95. Most rough
or painted surfaces also have fairly high emissivity values.
FIVE WAYS TO DETERMINE EMISSIVITY
There are five ways to determine the emissivity of the
material, to ensure accurate temperature measurements:
1. Heat a sample of the material to a known temperature,
using a precise sensor, and measure the temperature using
the IR instrument. Then adjust the emissivity value to force
the indicator to display the correct temperature.
2. For relatively low temperatures (up to 500°F), a piece of
masking tape, with an emissivity of 0.95, can be measured.
Then adjust the emissivity value to force the indicator to
display the correct temperature of the material.
3. For high temperature measurements, a hole (depth of which
is at least 6 times the diameter) can be drilled into the object.
This hole acts as a blackbody with emissivity of 1.0. Measure
the temperature in the hole, then adjust the emissivity to force
the indicator to display the correct temperature of the material.
4. If the material, or a portion of it, can be coated, a dull
black paint will have an emissivity of approx. 1.0. Measure
the temperature of the paint, then adjust the emissivity to
force the indicator to display the correct temperature.
5. Standardized emissivity values for most materials are
available (see pages 114-115). These can be entered into
the instrument to estimate the material’s emissivity value.
SPECTRAL RESPONSE
What is spectral response, and how will it affect my readings?
The spectral response of the unit is the width of the infrared
spectrum covered. Most general purpose units (for
temperatures below 1000°F) use a wideband filter in the 8 to
14 micron range. This range is preferred for most
measurements, as it will allow measurements to be taken
without the atmospheric interference (where the atmospheric
temperature affects the readings of the instrument). Some
units use wider filters such as 8 to 20 microns, which can be
used for close measurements, but are ‘‘distance-sensitive’’
against longer distances. For special purposes, very narrow
bands may be chosen. These can be used for higher
temperatures, and for penetrations of atmosphere, flames,
and gases. Typical low band filters are at 2.2 or 3.8 microns.
High temperatures above 1500°F are usually measured with
2.1 to 2.3 micron filters. Other bandwidths that can be used
are 0.78 to 1.06 for high temperatures, 7.9 or 3.43 for limited
transmissions through thin film plastics, and 3.8 microns to
penetrate through clean flames with minimum interference.
TEMPERATURE MEASUREMENT THROUGH GLASS
I want to measure the temperature through a glass or quartz
window; what special considerations are there?
Transmission of the infrared energy through glass or quartz
is an important factor to be considered. The pyrometer must
have a wavelength where the glass is somewhat transparent,
which means they can only be used for high temperature.
Otherwise, the instrument will have measurement errors
due to averaging of the glass temperature with the desired
product temperature.
MOUNTING
How can I mount the infrared pyrometer?
The pyrometer can be of two types, either fixed-mount or
portable. Fixed mount units are generally installed in one
location to continuously monitor a given process. They
usually operate on line power, and are aimed at a single
point. The output from this type of instrument can be a local
or remote display, along with an analog output that can be
used for another display or control loop.
Battery powered, portable infrared ‘‘guns’’ are also available;
these units have all the features of the fixed mount devices,
usually without the analog output for control purposes.
Generally these units are utilized in maintenance, diagnostics,
quality control, and spot measurements of critical processes.
RESPONSE TIME
What else should I take into account when selecting and
installing my infrared measurement system?
First, the instrument must respond quickly enough to process
changes for accurate temperature recording or control.
Typical response times for infrared thermometers are in
the 0.1 to 1 second range. Next, the unit must be able to
function within the environment, at the ambient temperature.
Other considerations include physical mounting limitations,
viewing port/window applications (measuring through glass),
and the desired signal processing to produce the desired
output for further analysis, display or control.
|